The Chichester Shutters
Showroom Experience
With lots of different materials, styles and options to consider, choosing shutters for your home can be a bit of a minefield!
That’s why a visit to our showroom is a great first step to exploring shutters.
Experience how much light they let in, how much privacy you really get and out unique fitting system that doesn’t use screws.
Address: Kingley Centre, Downs Road, West Stoke PO18 9HJ
Opening Hours: Tuesday – Saturday, 10am – 3.30pm
Please book an appointment below or call ahead of your visit.
Saturdays are by appointment only.
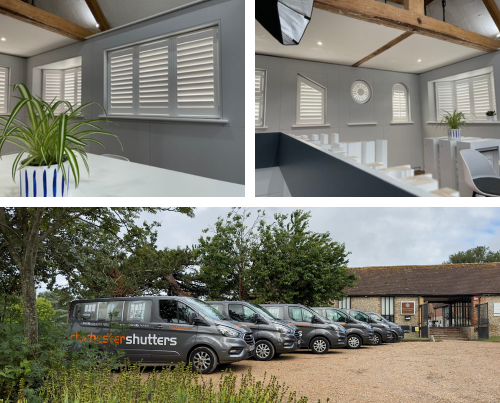
Top Tip! Bring some photos & rough sizes with you for tailored advice for your windows.
The Chichester Shutters showroom experience is more like a personal shopping appointment.
You will be 1-on-1 with a member of the team who will demonstrate everything with the use of samples & photos from previous installations.
During the appointment, we’ll explore:
- How the shutters will sit in the windows and fold open
- Which louvre size will work best and the split tilt feature
- The best colour for shutters to make your rooms brighter
- How much light they block out at night & the blackout upgrade
- Which material is most suitable for your windows
- Warranties, lead times & temporary blind solutions
- An estimated price based on rough sizes/photos you bring with you
- Plus, any specific tailored advice you require for your windows!
It really it the very best first step to exploring shutters so come see us soon!